Table of contents:
Understanding the Function of Harmonic Reducers in Robotics
How RV Reducers Benefit from Specialized Bearing Designs
Comparative Analysis: Harmonic vs. RV Reducer Bearings
Case Studies: Successful Implementations of Specialized Reducer Bearings
Understanding the Function of Harmonic Reducers in Robotics
Harmonic reducers are widely used in robotics due to their high precision, high reduction ratio, and compact structure. These reducers enable precise motion control and flexibility, making them ideal for robots such as humanoids and quadrupeds. Harmonic reducers rely on cross roller bearings and flexible bearings to deliver consistent and accurate movement. Cross roller bearings for harmonic reducers are designed to handle axial and radial loads, as well as overturning moments, enabling robots to maintain stability and precision. The four main series for harmonic reducers include CSG (CSF), CSD, SHG (SHF), and SHD types, each with unique features for specific robotic applications. Their ability to ensure smooth and stable rotation enhances the movement of robot joints and core mobility components.
How RV Reducers Benefit from Specialized Bearing Designs
RV reducers, known for their high rigidity and load-bearing capabilities, are integral to industrial robotic applications. They are equipped with angular contact ball bearings, designed to withstand heavy loads with minimal vibration. By incorporating such specialized bearings, RV reducers enhance the strength and reliability of robots in industrial and heavy-duty tasks. The lightweight and durable nature of these bearings also helps reduce inertia, improving overall energy efficiency. These advanced designs allow RV reducers to support the demanding operational requirements of robots used in manufacturing, assembly, and similar environments.
Comparative Analysis: Harmonic vs. RV Reducer Bearings
Harmonic reducers and RV reducers each rely on their specialized bearings to achieve optimal performance, but their applications differ. Cross roller bearings used in harmonic reducers are structured to handle multi-directional loads, making them ideal for humanoid robots and applications demanding high precision. On the other hand, RV reducers benefit from angular contact ball bearings, which are engineered for heavy-duty operations in industrial robots. This difference in bearing design and application highlights the importance of selecting the right type of reducer and bearings based on the specific needs of the robot. For example, while harmonic reducers facilitate delicate and precise movements, RV reducers are more suited for tasks requiring high torque and load capacity.
Case Studies: Successful Implementations of Specialized Reducer Bearings
The application of specialized bearings in harmonic and RV reducers is evident in the advancements of humanoid robots and robot dogs. These bearings, like those designed by Arorotech, have given robots the ability to carry out complex movements with unprecedented stability and precision. For example, in humanoid robots, harmonic reducer bearings enable fluid waist and arm rotations, which are essential for human-like motion. Similarly, robot dogs benefit from these bearings in their hip and knee joints, allowing them to maintain balance and mobility under high-frequency shocks and complex loads. These case studies demonstrate how premium bearing suppliers and ball bearing manufacturer contribute to the evolution of robotics, ensuring stability, efficiency, and long-term durability.
The precision, rigidity, and reliability of harmonic and RV reducers are directly influenced by their bearings. Specialized bearings, such as those provided by Arorotech, enable robots to achieve the precision, speed, and stability required for both industrial and innovative applications. The collaboration between leading bearing suppliers and the robotics industry continues to push the boundaries of what robots can achieve. When selecting bearings for your robotic projects, consult a trusted bearing supplier to ensure your components meet the demanding requirements of modern robotic applications.
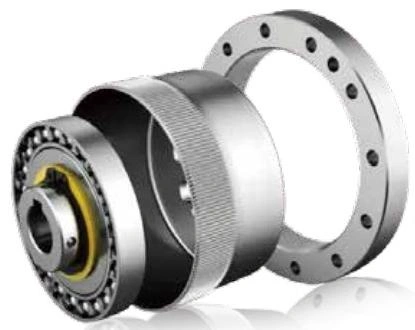
No comments:
Post a Comment